Kalibriermethode zur Prüfung der Schmitzring-Anpresskraft
Zielstellung
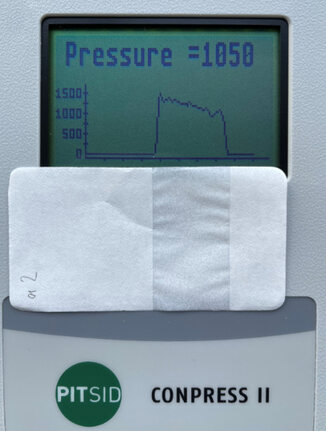
Ziel des Projektes war die Entwicklung einer neuen Kalibriermethode für das Pressungsprüfgerät CONPRESS II. Das Pressungsprüfgerät wird genutzt, um die Vorspannung zwischen aufeinander ablaufenden Schmitzringen in Druckmaschinen zu bestimmen. Diese befinden sich bei Bogenoffsetmaschinen seitlich an den Druckplatten- und Gummituchzylindern und dienen dazu, Belastungsschwankungen beim Überrollen des Plattenkanals zu reduzieren und damit eine hohe Druckqualität sicherzustellen. Bei der Montage der Maschine sowie nach Reparaturarbeiten muss die Pressung der Schmitzringe kontrolliert und eingestellt werden.
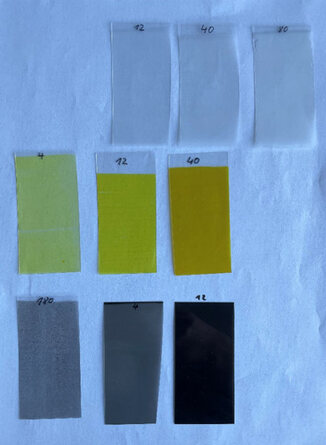
Zur Ermittlung der Schmitzringvorspannung wird ein Prüfstreifen aus Feinpapier auf die Schmitzringe aufgelegt und teilweise überrollt. Die hohe Pressung führt dazu, dass sich das Gefüge des Feinpapiers dauerhaft ändert und die Lichtdurchlässigkeit vergrößert wird. Die Differenz in der Opazität des Papierstreifens wird als Maß für die Vorspannung ausgewertet.
Zur Kalibrierung sollen in Zukunft Normale verwendet werden, die aus beständigem Material, vorzugsweise Kunststofffolie und damit nicht aus dem zur Messung verwendeten Feinpapier, bestehen. Diese Normale müssen deshalb definierte Opazitäten bzw. definierte Differenzen der Opazität zwischen Mess- und Referenzbereich aufweisen.
Ergebnisse
Grundlage der neuen Methode ist eine Auswahl spezieller Folienstreifen, welche im Detektionsbereich des Messgerätes in einem Wellenlängenbereich zwischen 900 und 1000 nm fein abgestufte Transmissionswerte aufweisen. Für die Entwicklung waren zunächst ausführliche Untersuchungen an den bisher verwendeten Kalibrierstreifen notwendig. Die dabei gewonnenen Erkenntnisse dienten zur Auswahl geeigneter Folien. Die spektralen Untersuchungen erlauben zukünftig auch genauere Angaben zum Messbereich des CONPRESS. Alternative Anwendungsmöglichkeiten des Feinpapiers als Messmittel oder die Messbarkeit anwenderspezifischer Prüfstreifen lassen sich dadurch leichter beurteilen.
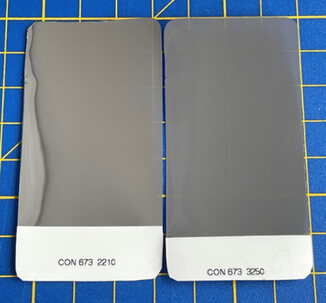
Die Transparenzwerte der industriell gefertigten Folien werden bereits beim Herstellungsprozess festgelegt. Eine nachträgliche Bearbeitung (z. B. Pressung oder Beschichtung) ist nicht notwendig. Die gewünschte feine Abstufung wird durch Kombination verschiedener Folien erreicht. Auch eine Kalibrierung auf Referenzwerte, die durch Pressung des Feinpapiers nicht erreicht werden können, ist damit möglich. Der Kalibrierprozess wurde vollkommen neu gestaltet und dabei so modifiziert, dass auf den einzelnen Streifen keine Transparenzunterschiede vorhanden sein müssen.
Die neue Kalibriermethode wird schrittweise bei der Auslieferung neuer und der Wartung gebrauchter Geräte in die Praxis überführt.
Um den Anwendern die Beurteilung der Funktionsfähigkeit des CONPRESS zu ermöglichen, ist vorgesehen, jedem Messgerät zukünftig eine Auswahl individueller Referenzstreifen beizulegen. Ein schleichender Empfindlichkeitsverlust des Geräts durch Alterung oder Verschmutzung kann so rechtzeitig erkannt werden.
Projektlaufzeit: Februar 2021 bis September 2022