Bestimmung der Lackschichtdicke auf Drucksubstraten
Ausgangssituation
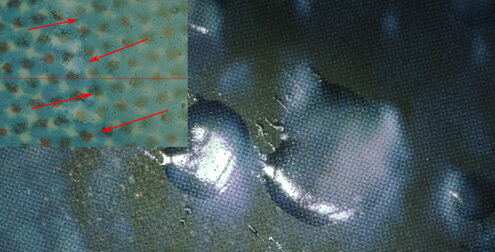
Zur Prozess- und Qualitätskontrolle an Druckmaschinen ist es notwendig, die Menge bzw. Dicke des auf das Substrat übertragenen Mediums genau einzustellen und zu kontrollieren. Für lasierende Druckfarben gibt es seit langem entsprechende Mess- und Regelsysteme. Diese nutzen den Zusammenhang zwischen optischer Dichte und Schichtdicke, um mittels Densitometer oder Spektralfotometer die Farbschicht zu vermessen. Für transparente oder opake Medien (Lacke, Metallpigmentfarben, Deckweiß, …) existiert bisher kein entsprechendes System. Gerade diese Medien sind aber im Verpackungsbereich, der die am stärksten wachsende Branche der Druckindustrie umfasst, weit verbreitet. Neben dem Schutz und der Veredlung des Verpackungsmaterials werden u.a. auch die Barriereeigenschaften der Lacke genutzt, um z. B. die Diffusion von Mineralölbestandteilen aus dem Faltschachtelkarton in die verpackten Lebensmittel zu verhindern.
Die zu übertragende Lackmenge wird anhand von Maschineneinstellungen wie Drehzahl oder den Anpresskräften zwischen den Walzen vorgegeben. Beabsichtigte oder zufällige Änderungen der Prozessparameter können die Übertragung aber stark beeinflussen und so zu Abweichungen von der gewünschten Lackschichtdicke führen. Zu geringe Schichten können im Verpackungsbereich einen verminderten Schutz der Oberflächen der verpackten Ware zur Folge haben. Zu hohe Auftragsmengen wiederum können Probleme bei der Trocknung der Lacke sowie unnötige Materialkosten verursachen.
Bisherige Messverfahren
Bisher erfolgt die Kontrolle der Auftragsmenge am fertigen Produkt gravimetrisch. Die Gewichtszunahme des Substrats während des Lackierens wird also der aufgetragenen Lackmenge gleichgesetzt. Auf Grund der geringen Schichtdicke ist aber eine sehr genaue Wägung im mg-Bereich erforderlich. Der Feuchtigkeitseintrag in das Substrat oder der Restwassergehalt des Lackes können dabei zu erheblichen Messfehlern führen. Erfolgt der Lackauftrag inline (zusammen mit dem Druck) ist eine spätere Unterscheidung der Gewichtsanteile von Druckfarbe und Lack kaum noch möglich. Bei Glanzlacken wird oft auf den erreichten Glanz als Maß für die Schichtdicke zurückgegriffen. Eine Korrelation zwischen Glanz und Schichtdicke besteht aber nur in sehr engen Grenzen und nur bei ausgewählten Materialien. Mangels anderer Lösungen ist die Glanzmessung als Verfahren zur Beurteilung von Homogenität und Konstanz der übertragenen Lackmenge in die Abnahmerichtlinie (Technische Abnahme von Lackwerken an Bogenoffsetdruckmaschinen) aufgenommen worden. Allerdings nur unter der Bedingung, dass dabei streng definierte Materialien eingesetzt werden. Weitere Verfahren wie Tast- und Lichtschnitt, mikroskopische oder interferometrische Messungen sind nur für den Einsatz im Labor geeignet.
Entwicklungsziel
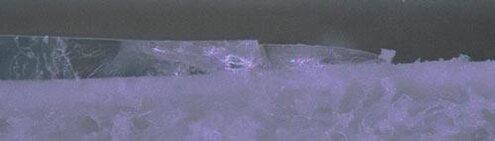
In diesem Projekt sollten die Grundlagen eines Messverfahrens entwickelt werden, das es ermöglicht, die Dicke einer transparenten oder opaken Lackschicht unter Produktionsbedingungen zu messen. Es sollte möglichst universell, unabhängig vom verwendeten Lack (Dispersions-, UV-, Drucklack) oder dem Drucksubstrat einsetzbar sein. Weiterhin bestanden sehr hohe Anforderungen an die Genauigkeit und Auflösung des Messverfahrens, da die zu bewertenden Lackschichten im Bereich weniger Mikrometer liegen.
Lösungsansatz
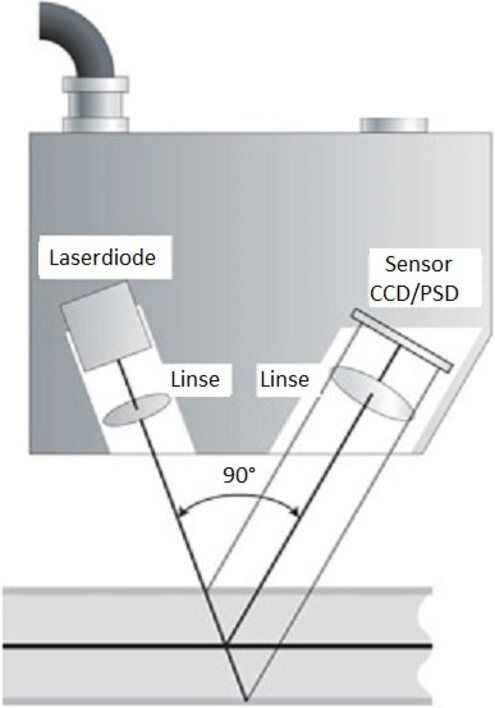
Im Projektverlauf wurden verschiedenste Messprinzipien hinsichtlich ihrer Anwendbarkeit für die beschriebene Aufgabenstellung untersucht. Bevorzugt wurden dabei Verfahren, welche eine direkte Dickenmessung durch Detektion der Schichtgrenzen des Lackes ermöglichen. Damit sind einseitige, ortsaufgelöste Messungen möglich, die zudem relativ unempfindlich gegen Störungen (Schwingungen, Substratschwankungen usw.) sind.
Derartige Verfahren setzten die Reflexion der jeweiligen Messstrahlung (Ultraschall, Wärmeimpuls, Laserlicht) an der Lackoberfläche sowie an der Grenzschicht zum Substrat voraus. Die Schichtdicke wird dann durch Laufzeitmessung, positionssensitive Empfangselemente oder anhand von Interferenzen berechnet.
Als problematisch hat sich bei den meisten getesteten Verfahren die Schichtgrenze zum Substrat erwiesen. Dort konnte entweder keine definierte Reflexion erzeugt werden oder der Intensitätsunterschied zur Reflexion an der Lackoberfläche war so groß, dass keine Auswertung möglich war. Die Materialeigenschaften von Lack und Substrat schließen in diesen Fällen die Anwendung aus.
Die besten Ergebnisse konnten mit Lasertriangulationssensoren erzielt werden. Die Grenzen der Messfähigkeit werden hier hauptsächlich von der Auflösung des Empfängers und der Fokussierung des Laserstahls bestimmt. Neben der Schichtdicke beeinflusst aber auch die Brechung des Laserstrahls an der Grenzfläche zum Lack die Position des empfangenen Lichtes und muss daher bei der Ermittlung exakter Messwerte berücksichtigt werden. Nach der Analyse der Intensitätsverteilung des empfangenen Lichtes wurden Auswertealgorithmen entwickelt, die eine subpixelgenaue Positionsbestimmung auf dem Empfänger ermöglichen. So wurden auch aus teileweise überlagerten Reflexionen noch einzelne Intensitätsmaxima extrahiert und die Schichtdicke berechnet. Dadurch konnte die Messfähigkeit eines bereits existierenden Sensors deutlich verbessert werden. Die durch Brechung an der Grenzschicht verursachte Verschiebung des Messstrahls ist proportional zur Dicke der durchstrahlten Schicht. Auch wenn der Brechungsindex des Lackes nicht exakt bekannt ist, ist daher bei den zu messenden geringen Schichtdicken auch nur mit geringen Fehlern (<10%) zu rechnen. Mit bekanntem Brechungsindex oder einer vorherigen Kalibrierung auf einen speziellen Lack könnte aber auch diese Abweichung noch verringert werden.
Resultate
Im Ergebnis konnte gezeigt werden, dass mit Hilfe der Lasertriangulation die Messung transparenter Lackschichten auf Drucksubstraten auch im Bereich unter 10 µm möglich ist. Die Messgrenzen vorhandener Systeme können durch Auswahl hochauflösender Empfänger sowie einer optimierten Strahlgeometrie in den Mikrometerbereich verschoben werden. Zusätzlich sind durch geschickte Auswertung des Empfangssignals auch Messgenauigkeiten unterhalb der physischen Auflösung des Sensors zu erreichen.
Projektlaufzeit: Februar 2018 bis Dezember 2019
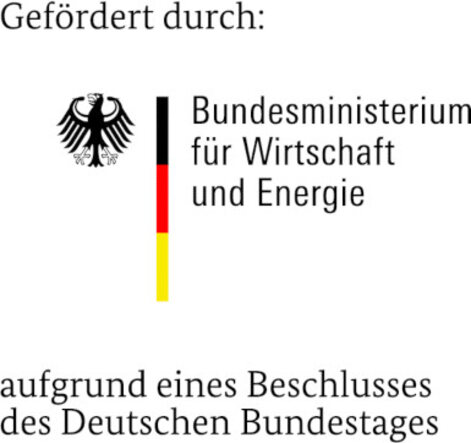
Mehr Informationen im
PDF-Download.